- Battery Manufacturing Equipment
- Battery Laboratory Assembly Equipment
- Battery Pack Assembly Equipment
- Sodium Ion Battery Manufacturing Equipment
- Solid State Battery Assembly Line
- Dry Electrode Assembly Equipment
- Supercapacitor Assembly Equipment
- Perovskite Solar Cell Lab Equipment
- Li ion Battery Materials
- Ni / Al / Cu Metal Foam
- Customized Electrode
- Cathode Active Materials
- Anode Active Materials
- Coin Cell Parts
- Lithium Chip
- Cylindrical Cell Parts
- Battery Current Collectors
- Battery Conductive Materials
- Electrolyte
- Battery Binder
- Separator and Tape
- Aluminum Laminate Film
- Nickel Strip/Foil
- Battery Tabs
- Graphene Materials
- Cu / Al / Ni / Stainless steel Foil
- Battery Laboratory Equipment
- Li ion Battery Tester
- Battery Safety Tester
- Battery Material Tester
- Film Coating Machine
- Rolling Press Machine
- Electrode Mixer
- Coin Cell Crimping Machine
- Coin Cell Electrode Disc Punching
- Pouch Cell Sealing Machine
- Pouch Cell Stacking Machine
- Pouch Cell Forming Machine
- Pouch Cell Ultrasonic Welder
- Pouch Cell Electrode Die Cutter
- Cylinder Cell Sealing Machine
- Cylinder Cell Grooving Machine
- Electrode Slitting Machine
- Cylinder Cell Winding Machine
- Cylinder Cell Spot Welding Machine
- Electrolyte Filling
- Type Test Cell
- Other Battery Making Machine
- NMP Solvent Treatment System
- Vacuum Glove Box
- Lab Furnaces
- Ball Mill
- Hydraulic Press
- Laboratory Equipment
1-600L Stirring Ball Mill Machine For Batch Production
Model Number:
TMAX-MBMCompliance:
CE certificateWarranty:
Two Year Limited Warranty With Lifetime SupportPayment:
T/T, Credit Card, Paypal, LC, Western UnionDelivery Time:
3 Days
Wechat:13506084915
1-600L Stirring Ball Mill Machine For Batch Production
Introduction
The principle of the stirring ball mill is driven by the spindle to rotate the mixer at high speed, so that the grinding medium in the stirring drum does irregular movement, this disorderly movement produces the collision, extrusion, friction and shear of the grinding medium, so that the material is crushed and finely ground, the whole machine is mainly composed of the stirring drum, stirring device, frame and electrical control and other auxiliary devices (such as: Material pumping circulation device, water-cooled jacket device, heating temperature control device, etc.) composition, especially suitable for small test, pilot test, large quantities of material wet grinding, grinding efficiency is high, grinding particle size is small, dry grinding is suitable for certain characteristics of the material, such as the material to have a certain fluidity, not easy to plate, bottom sticky wall, can achieve a good variety of process parameters requirements. Laboratory drum ball mill
Application
Simple equipment, small footprint, low energy consumption, low price and other advantages, is the preferred equipment for schools, scientific research units to carry out small batch experiments, widely used in zirconium silicate, zirconium oxide, electronic materials, magnetic materials, coatings, graphite pharmaceutical and other ultra-fine powder production field.
Characteristics
1. The equipment has simple structure, low noise, convenient handling, and does not occupy the working environment space.
2. Compared with other ball mill principles, because the mill has different running track curves in the stirring barrel, higher stirring speed, low power consumption, and high ball mill efficiency.
3. Material granularity by optimizing different ball ratio, speed, milling time and other related processes to control the curve distribution of its material fineness, the operation is very flexible and practical.
4. According to the requirements of material characteristics, customized heating temperature control device can be selected to control the heating range of the material, water cooling jacket device to control the material cooling, and material pumping circulation device to control the particle size of the ball mill material.
5. Through electrical control to achieve total timing, interval downtime or continuous, speed regulation cycle to achieve various process requirements of materials.
6. Equipment customizable materials Vacuum inert gas protection in the ball milling process in the stirring drum to prevent the material from being oxidized, and even flammable and explosive materials can be customized according to the explosion-proof requirements of customized equipment.
7. According to the requirements of material characteristics, the inner wall of the stirring barrel can be lined with non-metallic materials (corundum ceramic, zirconia, nylon, PTFE, polyurethane, etc.), and the stirring rod is outfitted with different materials to reduce the probability of material contamination and improve the purity of the material. Roller ball mill
Technical parameters
Name |
Volume (L) |
Power supply (V) |
Speed (rpm) |
Speed regulation mode |
Loading volume (L) |
MBM-1L |
1 |
Single phase 220V/50Hz |
50-1400 |
Frequency conversion |
0.3 |
MBM-2L |
2 |
Single phase 220V/50Hz |
50-1400 |
Frequency conversion |
0.6 |
MBM-3L |
3 |
Single phase 220V/50Hz |
50-1400 |
Frequency conversion |
1 |
MBM-5L |
5 |
Single phase 220V/50Hz |
60-560 |
Frequency conversion/constant speed |
1.6 |
MBM-10L |
10 |
Single phase 220V/50Hz |
60-560 |
Frequency conversion/constant speed |
3.3 |
MBM-15L |
15 |
Single phase 220V/50Hz |
60-380 |
Frequency conversion/constant speed |
5 |
MBM-20L |
20 |
Single phase 220V/50Hz |
60-380 |
Frequency conversion/constant speed |
6.6 |
MBM-30L |
30 |
Single phase 220V/50Hz |
60-310 |
Frequency conversion/constant speed |
10 |
MBM-50L |
50 |
3 phase 380V/50Hz |
60-140 |
Frequency conversion/constant speed |
16.6 |
MBM-100L |
100 |
3 phase 380V/50Hz |
60-140 |
Frequency conversion/constant speed |
33.3 |
MBM-200L |
200 |
3 phase 380V/50Hz |
60-110 |
Frequency conversion/constant speed |
66.6 |
MBM-300L |
300 |
3 phase 380V/50Hz |
60-110 |
Frequency conversion/constant speed |
100 |
MBM-500L |
500 |
3 phase 380V/50Hz |
60-90 |
Frequency conversion/constant speed |
166.6 |
MBM-600L |
600 |
3 phase 380V/50Hz |
60-90 |
Frequency conversion/constant speed |
200 |
Name |
Motor power (KW) |
Barrel material |
Feed size (um) |
Output size (um) |
Note |
MBM-1L |
0.37 |
Hard carbon, stainless steel, cemented carbide, ceramic corundum, zirconia, agate, nylon, Teflon, polyurethane |
≤5 (More brittle material) |
≤1 |
The relevant parameters are for reference only, and can be customized according to the customer's process requirements and different properties of the material |
MBM-2L |
0.37 |
||||
MBM-3L |
0.37 |
||||
MBM-5L |
0.75 |
||||
MBM-10L |
1.5 |
≤10 (More brittle material) |
|||
MBM-15L |
2.2 |
||||
MBM-20L |
2.2 |
||||
MBM-30L |
3 |
||||
MBM-50L |
4 |
||||
MBM-100L |
7.5 |
≤15 (More brittle material) |
|||
MBM-200L |
11 |
||||
MBM-300L |
15 |
||||
MBM-500L |
18.5 |
||||
MBM-600L |
22 |
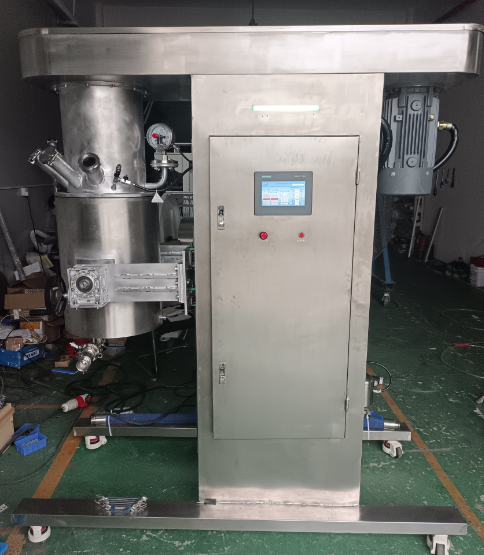